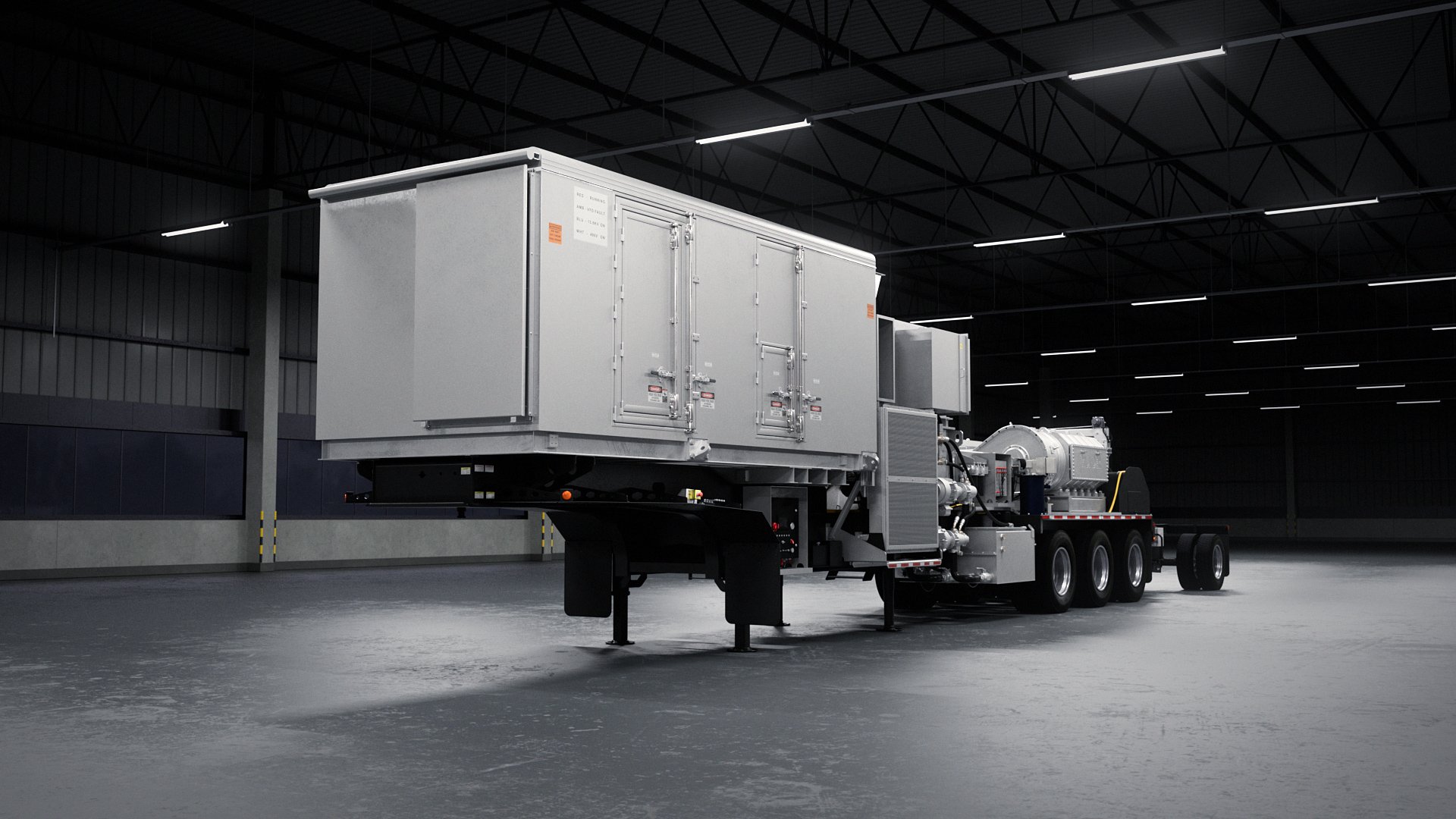
Case Study: Electric Frac Pump
Meet the next generation of sustainable fracturing technology
Project Highlights
Horsepower
Barrels per Minute
Emissions
01. Problem
Conventional 100% diesel-powered frac pumpers produce the highest emissions, they are costly to operate due to maintenance and fuel costs, and they are limited to less than 3000 hp in most cases.
02. Objective
Develop a more power dense, low emission, diesel alternative with fewer moving parts.
03. Solution
THOR: a fully electric, zero-emissions fracturing pumper with 40,000-hour Hitachi motor and 5,000-horsepower capability.
04. Result
EnQuest’s “THOR” eFrac pump is a compact, powerful, reliable, and emissions-friendly solution that can meet operators’ toughest performance and ESG targets.
Background
Conventional hydraulic fracturing has depended on diesel fuel to power the pumps to sufficiently high flow rates and pressures to release trapped oil deposits from rock. However, despite their reputation for durability, diesel engines come with a number of drawbacks.
A typical diesel frac fleet consumes 7 million-plus gallons of diesel and emits 70,000 metric tonnes of carbon dioxide per year. Remote sites often require 700,000 tanker truck loads to replenish fuel to the frac equipment. When the price of diesel rises, the cost to fuel a traditional fleet can quickly reach $10,000 per hour.
Diesel-powered pumps are also extremely large, creating both crowded site conditions and safety hazards.
And finally, even though diesel engines and transmissions require less maintenance than gas models, they still have to be serviced more often than electric motors, transformers, and variable frequency drives.
EnQuest’s Answer
Based on our consultations with major fracturing service providers and leading equipment makers, we developed plans for an all-electric frac pump that would have a much smaller footprint than a conventional model without sacrificing performance. A significant challenge was achieving the proper weight distribution of the body and equipment to work with our desired chassis. We had to assure compliance with bridge laws and gross axle weight ratings.
In the end, our unit’s smaller size was made possible by being hyper-efficient due to being powered by gas turbines, instead of diesel, thus no need for an engine or transmission. We also included a removeable booster to the unit so that after arriving at the well site, it could be even more maneuverable. And 13.8 KV power inputs cut down on cable size and weight, as well.
But with 5,000-horsepower capacity, we knew this pump would have power aplenty, despite its smaller frame. In fact, it cuts the number of necessary pumps in half, making it perfect for simultaneously fracturing two wells at once. We named it THOR.
See THOR up close below…
Greener, Safer, Better
The ability to power a THOR fleet’s operation off of a single natural gas turbine or multiple natural gas engine generators offers enormous carbon emissions reductions to diesel, as well as significant cost savings by blending stranded field gas on-site. Natural gas that would otherwise be flared into the atmosphere can be captured and used to power the equipment for both sustainability and profitability boosts.
THOR was also built with safety in mind, with cable trays and guards included to protect the medium-voltage cabling and connections from being stepped on or cut.
Even the well site becomes safer, as the quieter, electric-motor operation lowers noise, a notorious problem and potential health hazard associated with conventional frac units. And risk factors such as diesel truck logistics and excess gas handling are removed from the picture, as well.